What Are Miler Welds And Why Are They Essential For Modern Manufacturing?
Miler welds have become a cornerstone of modern manufacturing, offering unparalleled precision and durability in metal fabrication. These specialized welding techniques are widely recognized for their ability to join metals seamlessly, creating strong bonds that withstand the test of time. Whether you're in the automotive, aerospace, or construction industry, miler welds play a critical role in ensuring the structural integrity of components. Their versatility and adaptability to various materials make them indispensable for industries that demand high-performance results.
With advancements in technology, miler welds have evolved to meet the ever-growing demands of precision engineering. Manufacturers rely on these techniques to produce lightweight yet robust structures, reducing material waste while enhancing product longevity. This has not only improved efficiency but also contributed to sustainable manufacturing practices. As industries continue to innovate, miler welds remain at the forefront of cutting-edge solutions.
Understanding the intricacies of miler welds can empower professionals and enthusiasts alike to appreciate their significance. From their applications in everyday products to their role in groundbreaking projects, miler welds are more than just a technical process—they are a testament to human ingenuity. In this article, we’ll explore their origins, applications, and future potential, shedding light on why they are so vital in today’s world.
Read also:Discovering The Joys Of Family Adventures Why Buscar Kid And Mom Is Essential For Modern Families
Table of Contents
- What Are Miler Welds and How Do They Work?
- Applications of Miler Welds in Various Industries
- What Are the Different Types of Miler Welds?
- Why Are Miler Welds Preferred Over Other Techniques?
- What Challenges Are Associated with Miler Welds?
- The Future of Miler Welds: Innovations and Trends
- How Can You Master the Art of Miler Welds?
- Frequently Asked Questions About Miler Welds
What Are Miler Welds and How Do They Work?
Miler welds are a specialized category of welding techniques designed to join metals with exceptional precision and strength. These welds are created using advanced equipment and processes that ensure the integrity of the bond while minimizing defects. At their core, miler welds rely on the principle of fusion, where heat is applied to melt the base metals, allowing them to merge seamlessly. This process is often supplemented with filler materials to enhance the bond’s durability.
One of the defining characteristics of miler welds is their adaptability to different materials, including stainless steel, aluminum, and titanium. This versatility makes them suitable for a wide range of applications, from intricate aerospace components to heavy-duty construction projects. The process involves meticulous control over parameters such as temperature, pressure, and welding speed, ensuring that the final product meets stringent quality standards.
Moreover, miler welds are often performed using automated systems, which enhance consistency and reduce human error. These systems are equipped with sensors and monitoring tools that provide real-time feedback, allowing operators to make adjustments on the fly. This level of precision not only improves the quality of the welds but also reduces material waste, making the process more cost-effective and environmentally friendly.
Applications of Miler Welds in Various Industries
Miler welds are utilized across numerous industries, each benefiting from their unique properties. In the automotive sector, these welds are integral to the production of vehicle frames, exhaust systems, and engine components. Their ability to create lightweight yet strong structures has revolutionized car manufacturing, enabling the production of fuel-efficient vehicles without compromising safety.
In the aerospace industry, miler welds are indispensable for constructing aircraft components that must withstand extreme conditions. From turbine blades to fuselage panels, these welds ensure the structural integrity of parts that are subjected to high stress and temperature variations. Similarly, the construction industry relies on miler welds for building bridges, pipelines, and skyscrapers, where durability and reliability are paramount.
Other industries, such as electronics and medical devices, also benefit from miler welds. For instance, these techniques are used to create intricate circuits and surgical instruments, where precision is critical. By tailoring the welding process to specific requirements, manufacturers can achieve results that meet the highest standards of quality and performance.
Read also:Discover The Inspiring Journey Of Lyra Crow A Rising Star
What Are the Different Types of Miler Welds?
Miler welds encompass a variety of techniques, each suited to specific applications and materials. Understanding the differences between these methods can help manufacturers choose the right approach for their needs.
TIG Welding: Precision at Its Finest
Tungsten Inert Gas (TIG) welding is a popular method within the miler welds category, known for its precision and control. This technique uses a non-consumable tungsten electrode to produce the weld, with an inert gas like argon shielding the weld area from contamination. TIG welding is ideal for thin materials and complex geometries, making it a favorite in industries like aerospace and automotive.
One of the key advantages of TIG welding is its ability to produce clean, high-quality welds with minimal spatter. This makes it suitable for applications where aesthetics are important, such as custom metalwork and artistic projects. However, TIG welding requires a high level of skill and is generally slower than other methods, which can impact productivity.
MIG Welding: Speed Meets Efficiency
Metal Inert Gas (MIG) welding, on the other hand, is known for its speed and efficiency. This technique uses a consumable wire electrode that serves as both the filler material and the electrode, making it ideal for high-volume production. MIG welding is commonly used in the construction and manufacturing sectors, where speed and cost-effectiveness are priorities.
While MIG welding may not offer the same level of precision as TIG welding, it excels in versatility and ease of use. It can be applied to a wide range of materials and thicknesses, making it a go-to choice for many industrial applications. Additionally, advancements in MIG welding technology have improved its ability to produce high-quality welds, bridging the gap between speed and precision.
Why Are Miler Welds Preferred Over Other Techniques?
Miler welds offer several advantages that set them apart from traditional welding methods. One of the most significant benefits is their ability to create strong, durable bonds that can withstand extreme conditions. This makes them ideal for applications where safety and reliability are critical, such as in the aerospace and automotive industries.
Another advantage of miler welds is their precision. These techniques allow for tight control over the welding process, minimizing defects and ensuring consistent quality. This level of precision is particularly important for industries that require intricate designs or work with sensitive materials. Additionally, miler welds are often more environmentally friendly than other methods, as they reduce material waste and energy consumption.
Finally, miler welds are highly versatile, capable of working with a wide range of materials and thicknesses. This adaptability makes them suitable for a variety of applications, from heavy-duty construction projects to delicate medical devices. By offering a combination of strength, precision, and versatility, miler welds have become the preferred choice for many manufacturers.
What Challenges Are Associated with Miler Welds?
Despite their many advantages, miler welds are not without challenges. One of the primary issues is the high level of skill required to perform these techniques effectively. Whether it’s TIG or MIG welding, operators must undergo extensive training to master the nuances of the process, which can be time-consuming and costly.
Another challenge is the initial investment in equipment and technology. Advanced welding systems, particularly those used for miler welds, can be expensive to purchase and maintain. This can be a barrier for smaller businesses or startups looking to adopt these techniques. Additionally, the complexity of the equipment may require specialized maintenance, further increasing operational costs.
Finally, miler welds can be sensitive to environmental factors such as temperature and humidity. These conditions can affect the quality of the weld, leading to defects or inconsistencies. To mitigate these risks, manufacturers must implement strict quality control measures and invest in monitoring tools that provide real-time feedback.
The Future of Miler Welds: Innovations and Trends
The future of miler welds is bright, with ongoing innovations poised to revolutionize the industry. One of the most exciting trends is the integration of artificial intelligence (AI) and machine learning into welding systems. These technologies enable predictive maintenance, real-time monitoring, and automated adjustments, improving the efficiency and quality of miler welds.
Another promising development is the use of advanced materials in welding. As industries continue to explore new alloys and composites, miler welds are being adapted to work with these materials, pushing the boundaries of what is possible. This has significant implications for sectors like aerospace and renewable energy, where lightweight and durable materials are in high demand.
Finally, sustainability is becoming a key focus in the evolution of miler welds. Manufacturers are exploring ways to reduce energy consumption and material waste, aligning with global efforts to combat climate change. By adopting eco-friendly practices and technologies, the industry is paving the way for a more sustainable future.
How Can You Master the Art of Miler Welds?
Mastering miler welds requires a combination of theoretical knowledge and hands-on experience. For those looking to excel in this field, formal education and training programs are a great starting point. These programs provide a solid foundation in welding principles and techniques, preparing individuals for the challenges of the industry.
Practical experience is equally important, as it allows individuals to apply their knowledge in real-world scenarios. Internships, apprenticeships, and on-the-job training can provide valuable insights into the nuances of miler welds, helping individuals refine their skills. Additionally, staying updated on the latest trends and technologies is crucial for staying competitive in this rapidly evolving field.
Networking with industry professionals and joining welding associations can also be beneficial. These connections provide opportunities to learn from experts, share experiences, and stay informed about advancements in the field. By combining education, experience, and networking, individuals can position themselves for success in the world of miler welds.
Frequently Asked Questions About Miler Welds
What Are the Most Common Applications of Miler Welds?
Miler welds are widely used in industries such as automotive, aerospace, construction, and electronics. They are ideal for applications that require precision, strength, and durability.
How Do Miler Welds Compare to Traditional Welding Methods?
Miler welds offer superior precision, adaptability, and efficiency compared to traditional methods. They are particularly suited for complex geometries and sensitive materials.
Are Miler Welds Environmentally Friendly?
Yes, miler welds are more environmentally friendly than many traditional techniques, as they reduce material waste and energy consumption. Ongoing innovations are further enhancing their sustainability.
Learn more about welding basics and techniques from the American Welding Society.
Conclusion
Miler welds represent a cornerstone of modern manufacturing, offering unparalleled precision, strength, and versatility. From their applications in aerospace and automotive industries to their role in sustainable practices, these techniques continue to shape the future of metal fabrication. By understanding their intricacies and staying informed about innovations, professionals can harness the full potential of miler welds to drive progress and innovation.
StudentVue St Charles: A Comprehensive Guide To Accessing Your Academic Information
What Is Druski Net Worth In 2023? Discover The Journey Of A Rising Star
Exploring The Power Of My Chart Stormont: A Comprehensive Guide

Welds JToH Tower Developers Wiki
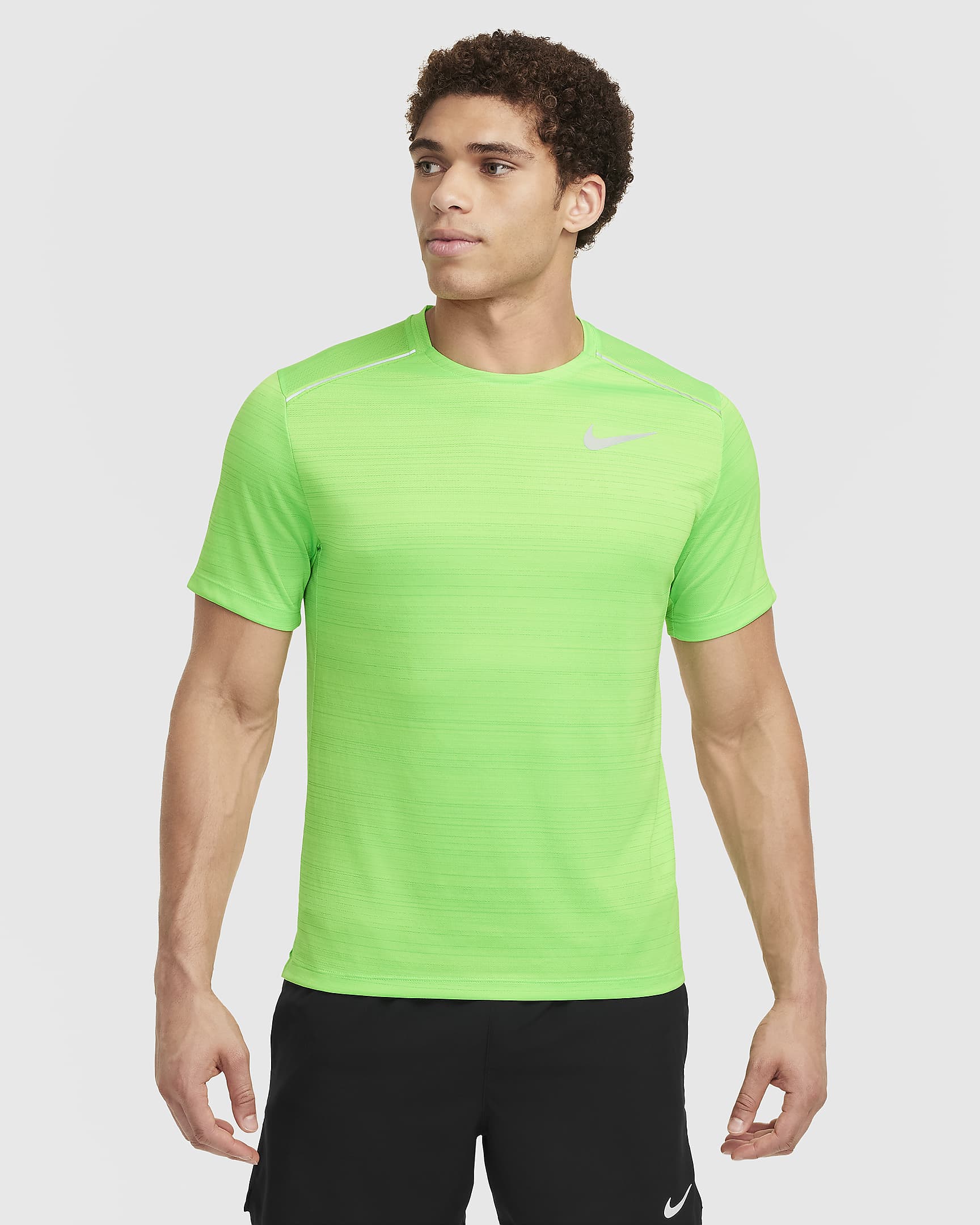
Nike Miler Men's ShortSleeve Running Top. Nike UK